High Purity Monoclinic Zirconia Powder From China Factory
- Zirconia ( Zro2 Powder) is a unique advanced ceramic
- Supply 99.5%,99.9% and 99.95% high purity Zro2 Powder with nano and micron particle size
- Strict quality control measures for ceramic raw materials and production
- kinga Ceramic offers zirconia compounds for injection molding
- Import raw materials zirconia sand from Australia
Get an Instant Quote
KINGA CERAMIC
Your High Purity ZrO2 Powder From China Suppliers
Kingda Ceramic is the leading manufacturer of high purity zirconia oxide powder in China. According to the different contents of ZrO2 , it is divided into four types ZrO2 powder, including 65%, 99.5%, 99.9% and 99.95% purity zirconia oxide powder.
Zirconia powder with different contents has completely different uses. Zirconia has potential for usage in a wide variety of applications – everything from bio ceramic, telecommunications to the new energy of the future and environmentally friendly products.
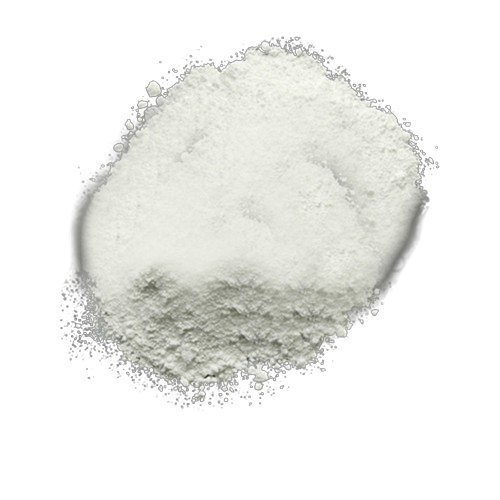
3mol Yttria Stabilized Zirconia
It is suitable for making ceramic zirconia elements, tubes, parts which ready to press, injection and moulding production process.
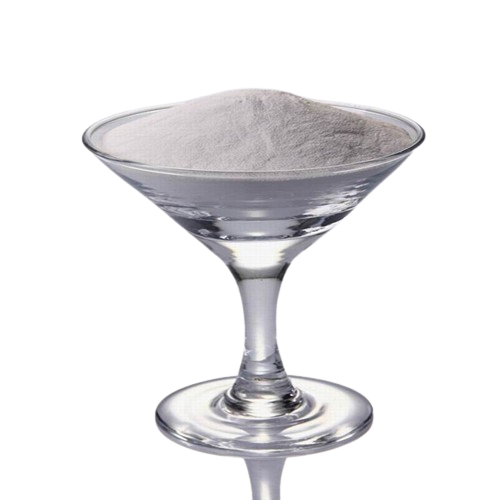
5% YSZ Zirconia Powder
It is made by chemical process and for fine avdanced ceramic that requires a high strong thermal shock resistance, fracture toughness, and superior corrosion resistance.
KINGDA CERAMIC – Leading Factory & Supplier Of Yttria Stabilized Zirconia Powder From China
- Helps customer to select right ysz powder
- Supply Ready to press powder and injection powder
- Provide tetragonal and cubic phase ysz powder
KINGDA Ceramic Grindig Media Beads
KINGDA CERAMIC mainly supply zirconia beads and alumina beads which are widely used for grinding, dispersing and polishing application in ceramic industries, such as UV and screen printing inks, coating,painting,electronic paste,raw material of lithium battery, pharmaceutical,biological,minerals and other nano products industries.
Check All Our Products
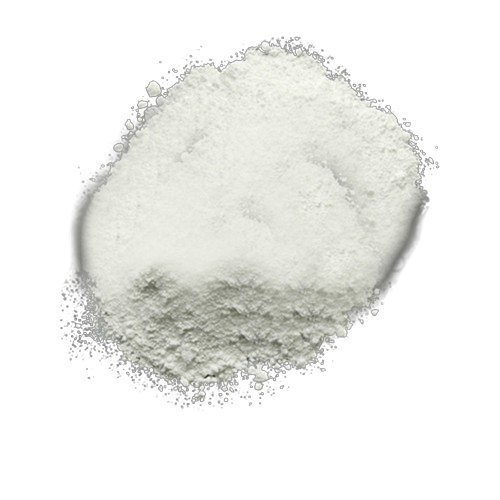
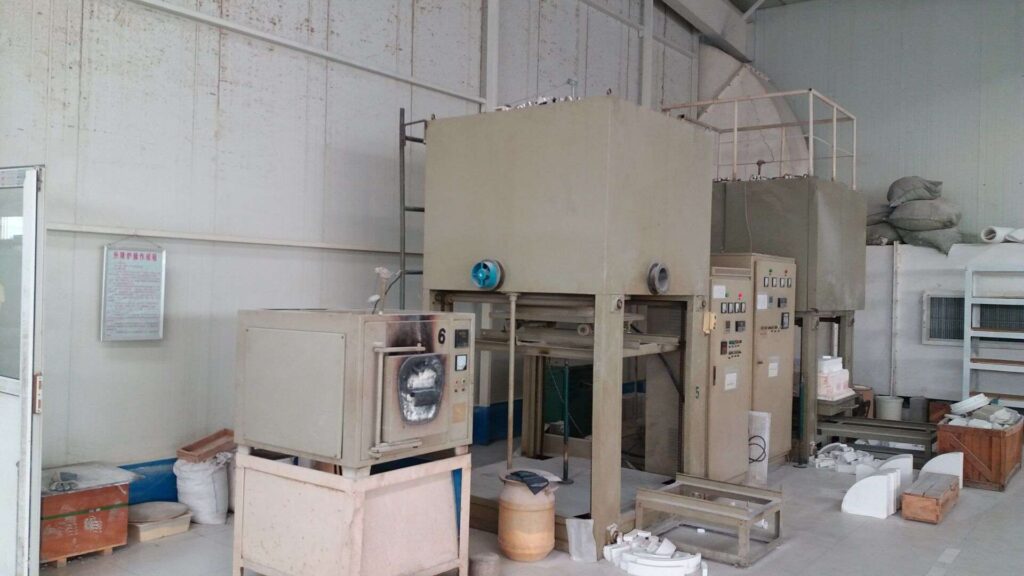
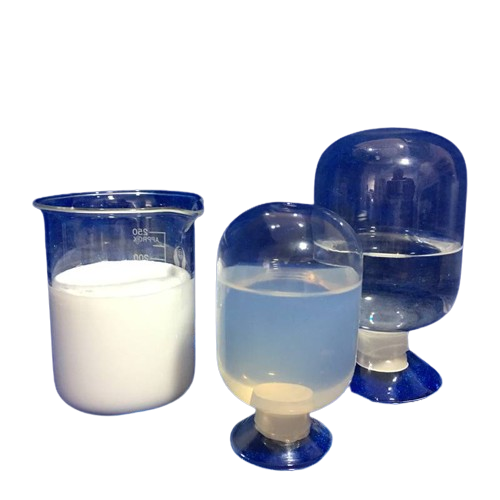
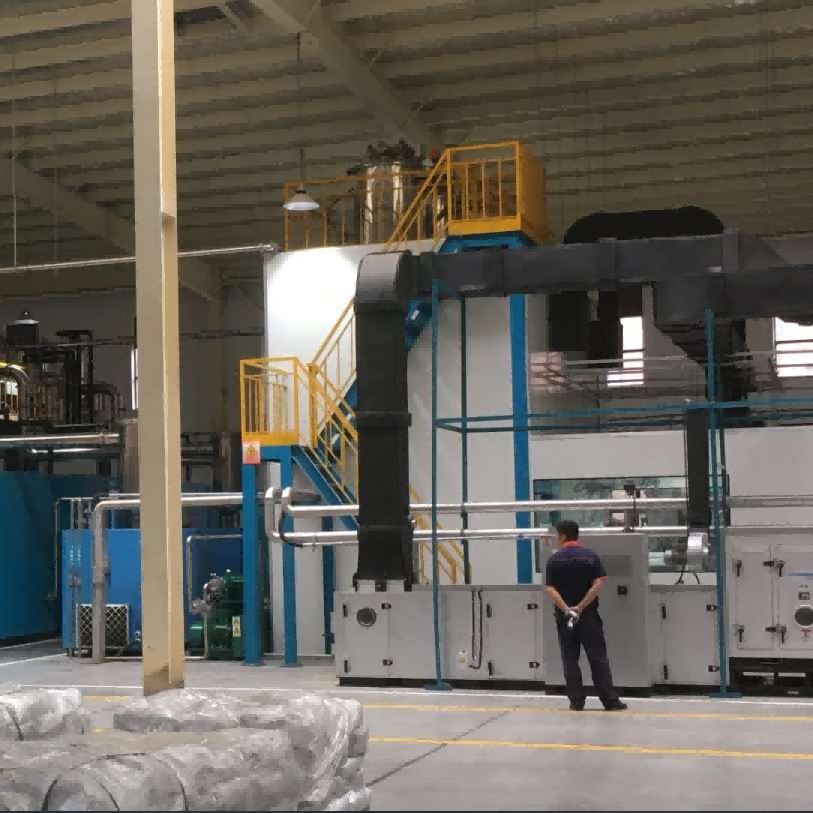
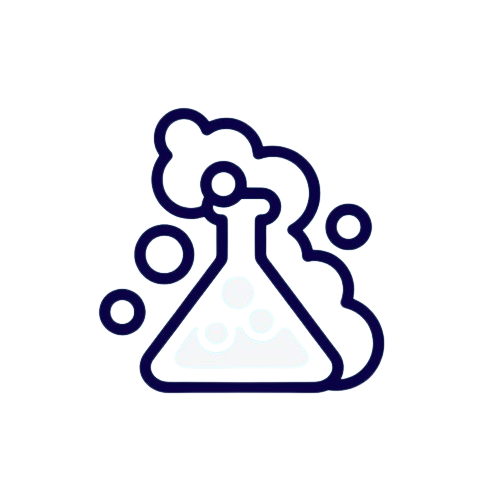
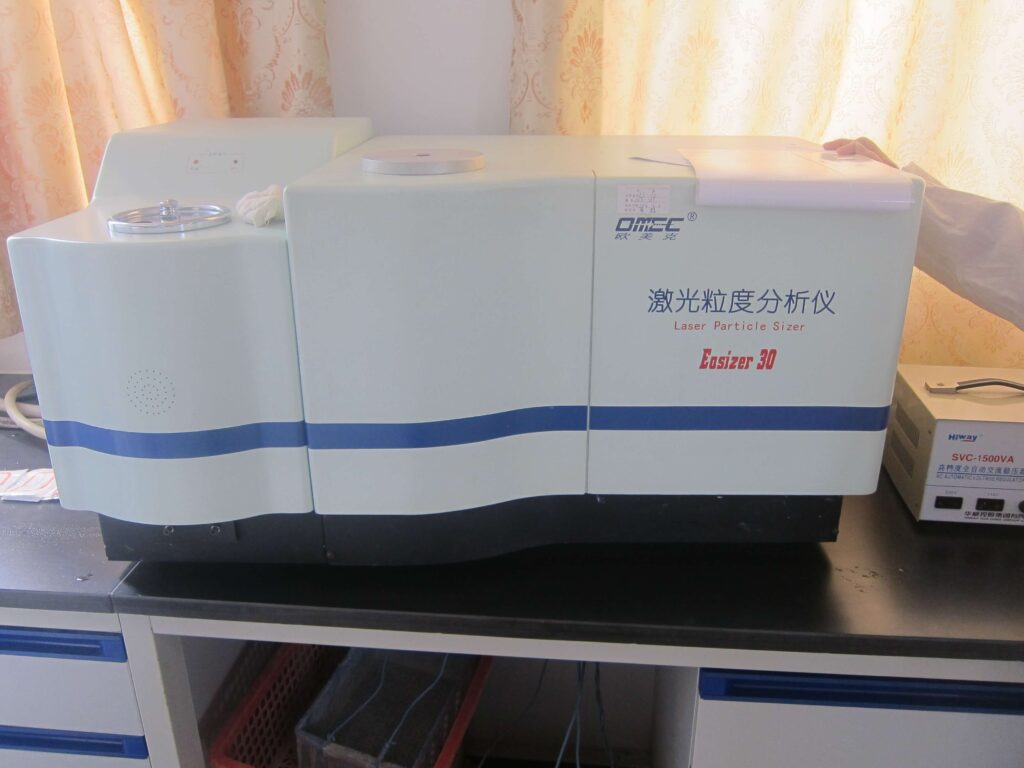
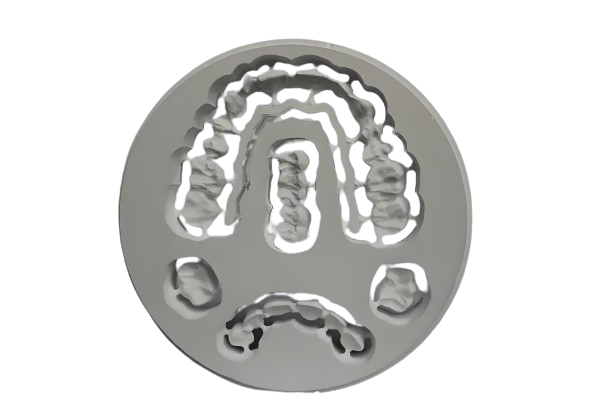
Making for dental block
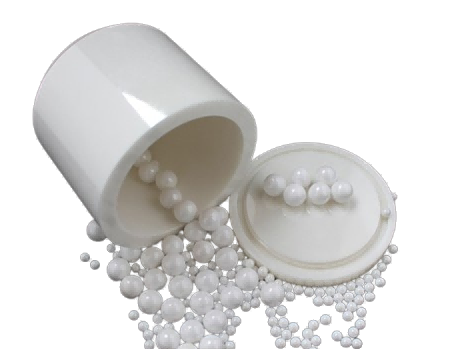
Making zirconia beads and zirconia jar
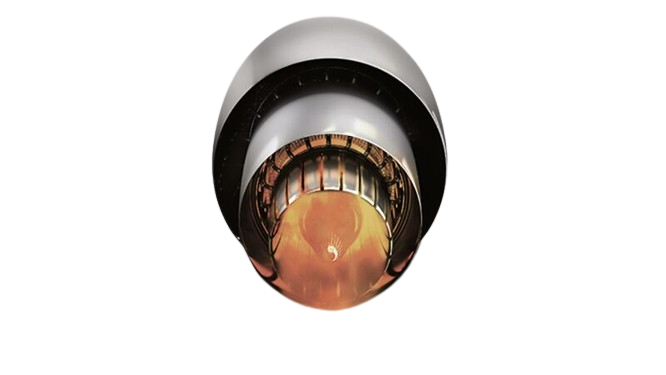
Making for thermal barrier coating
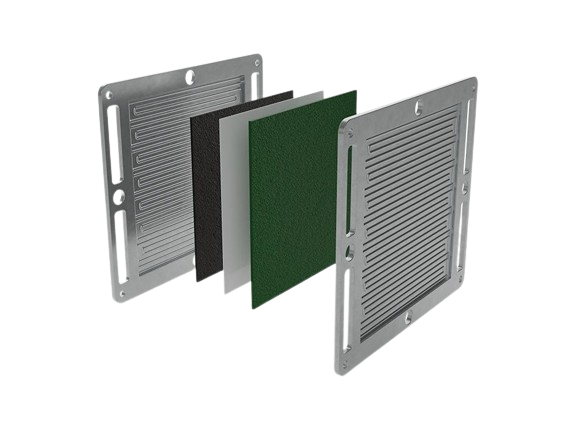
Making for solid oxide fuel cell
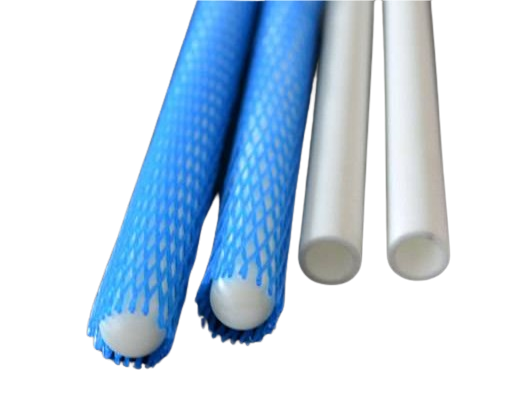
Making for zirconia ceramic tubes

Making for zirconia ceramic tubes
Frequently Asked Question for yttria stabilized zirconia powder
Is your company a yttria stabilized zirconia powder distributor or a manufacturer?
We are the professional manufacturer of YSZ powder in China.
What shape of your yttria stabilized zirconia powder?
We can provide hollow spherical granulation powder and irregular shape powder.
How is your payment term?
30% payment in advance and balance payment before shipment. For bulk order, we can do L/C or discuss the payment term case by case.
How is your production lead time?
The delivery time for ysz powder with regular particle sizes is within one week. For customized particle size will takes about 15 to 20 days.
Where is the port nearest to you?
Our nearest ports are Shenzhen,Guanzhou and Shanghai.
Yttria Stabilized Zirconia Powder Introduction
We supply ceramic powder which including zirconium oxide powder and yttria stabilized zirconia powder. In this introduction, the main focus is yttria stabilized zirconia powder with tetragonal phase and cubic teragonal.Among all ceramic oxide materials, tetragonal zirconia stabilized with the addition of 3mol% Y2O3 (Y-TZP) exhibits at room temperature the highest performance in terms of toughness,bending strength and corrosion resistance.
According to the content of yttria oxide, it can be divided into 3mol% (YSZ-3), 4mol%(YSZ-4) 5mol% (YSZ-5) and 8mol% Y2O3(YSZ-8).
3mol% , 4mol%, 5mol% yttria stabilized powder are belong to tetragonal phase.
8mol% yttria stabilized zirconia powder is belong to cubic phase.
Zirconium powder is belong to monoclic phase.
3mol YSZ powder includes 5% yttria and 95% zirconia. They are widely used in making zironia ceramic elments, yttria stabilized zirconia beads, dental block and other application.
4mol yttria stabilized zirconia powder means 7-8% yttria, balance is zirconia.That ceramic powder is usually used as a thermal spray coating for Top coat (insulating layer) in a thermal barrier coating(TBC) system for aerospace and gas turbine industries, such as combustion liners,transition pieces,after burners,gas turbine and airfoils and turbine ,heat shields. Thermal protection at temerature up to 900℃ (1650℉) metallic diesel and gasline engine such as cylinder heads,piston crown,turbocharges,exhaust and intake values.
As a ysz powder chinese supplier. Kingda Ceramic’s spheroidal powders with excellent flowability, chemical homogeneity, structural stability and high purity. Our high temp powder coat has excellent thermal shock and insulating features. Oerlikon Metco as top thermal barrier coating in the world, our plasma spray powder quality is very close to theirs.
8 mol Yttria stabilized zirconia powder includes about 13% yttria as stabilizer and balance is zirconia oxide.
8Y-YSZ powder is widely used as an electrolyte material in solid oxide fuel cells. It provides high ionic conductivity and stability at high temperatures, making it essential for efficient energy conversion in SOFCs.
Due to its biocompatibility and excellent mechanical properties, 8mol YSZ powder is also widely used in the production of dental crowns, bridges, and orthopedic implants. It offers high strength and wear resistance, ensuring durability and longevity.
As a ysz powder chinese suppliers, we can supply full range of yttria stabilized zirconia powder with stable quality and high purity to meet different customer and market demands.
Yttria Stabilzied Zirconia Powder FAQ Guide
1. What is the ceramic powder?
Ceramic powder is a wide range concept. Generally it is a finely ground material composed of inorganic, non-metallic substances that are typically used to produce ceramics through various manufacturing processes,such as molding, injection,dry precess,CIP,etc. These powders can be composed of oxides, carbides, nitrides, or other compounds, depending on the desired properties of the final ceramic product. Here are some key points about ceramic powder:
Composition:
- Oxides: Common oxide ceramic powders include alumina (Al₂O₃), zirconia (ZrO₂), and titania (TiO₂).
- Carbides: Silicon carbide (SiC) and boron carbide (B₄C) are examples of carbide ceramic powders.
- Nitrides: Silicon nitride (Si₃N₄) and aluminum nitride (AlN) are examples of nitride ceramic powders.
Properties:
- High Temperature Resistance: Ceramic powders can withstand extremely high temperatures, making them suitable for high-temperature applications.
- Hardness: Ceramics are typically very hard and wear-resistant.
- Chemical Stability: Many ceramics are chemically inert and resistant to corrosion.
- Electrical Insulation: Most ceramic materials are excellent electrical insulators, although some ceramics can also be semiconducting or superconducting.
Applications:
- Structural Ceramics: Used in applications requiring high strength and durability, such as cutting tools, bearings, and armor.
- Electronic Ceramics: Utilized in electronic components like capacitors, insulators, and substrates.
- Bioceramics: Employed in medical implants and prosthetics due to their biocompatibility.
- Thermal Barrier Coatings: Applied to protect components from high temperatures in engines and turbines.
- Catalysts and Supports: Used in catalytic converters and other chemical reaction processes.
Manufacturing Processes:
- Dry Pressing and Sintering: Powder is pressed into a desired shape and then heated to bond the particles together in electric kiln or other kind of high temperature sintering furnace.
- Injection and Molding: Ceramic powder is mixed with a binder and injected into a mold.
- Tape Casting: Thin layers of ceramic powder are cast into tapes, which are then laminated and fired.
- Additive Manufacturing: Also known as 3D printing, ceramic powders can be used to create complex shapes layer by layer.
Ceramic powders are integral to the production of a wide range of advanced ceramic materials and components, offering unique properties that make them essential in many industrial, technological, and medical applications.
Kingda Ceramic supply ceramic powder ,including zirconium powder and yttria stabilized powder with different content of ytrria as stabilizer.
2. What is the ysz density?
Zirconia is one of the most widely used ceramic materials, and it has three structurally different phases, such as monoclinic, tetragonal, and cubic phases, and the different phase contents can have a large impact on the properties of zirconia ceramic materials.
At present, the common ones are mostly yttria stabilised zirconia materials. Among them, 3Y-TZP (3% mol fraction, in fact Y2O3 content is about 5% percent) material has the best mechanical properties, and it is also the most commonly used class of zirconia ceramic materials, which has widely application prospects in different industries, such as chemical industry, machinery and so on. The properties of 3Y-TZP produced by different methods vary greatly. In order to obtain zirconia ceramic materials with high mechanical properties, controlled sintering temperature, impurities,doping etc. Adding additives can also change the grain size and phase composition of the material to some extent. Grain size and phase composition can have a significant effect on the physical properties of ceramic materials.
The molar fraction of yttrium oxide corresponding to maximum densification is 3%(real yttria content is about 5% percentage), and the relative density reaches the highest. Before the critical point, as the yttrium oxide content increases, the density of the sample gradually increases, and then gradually decreases after the critical point.
Obviously, the relative density of the sintered body with a yttria mole fraction of 3% yttria (real yttrium content is about 5% percentage) is higher than that of other groups, indicating that Y2O3 can promote the densification of zirconia during sintering. This is because the radius of Y3 (1.06A) is larger than that of Zr4 (0.87A). When Y2O3 forms a displacement solid solution with ZrO2, it distorts the lattice of the ZrO2 main crystal phase, increases defects, facilitates the movement of structural elements, and promotes sintering, thereby obtaining higher density. When the yttrium oxide content exceeds the critical value, the role of Y2O3 in the zirconia matrix weakens, and excessive Y2O3 hinders the crystallization process of zirconia sintering, resulting in a gradual decrease in relative density.
In addition, X-ray photoelectron spectroscopy (XPS) analysis showed that Y3 tends to cluster at grain boundaries, which strongly hinders the movement of grain boundaries and can prevent or delay the separation of pores and grain boundaries, thereby allowing the densification process to continue in the later stage of sintering. When the yttrium oxide content is 3% (mole fraction), this effect is maximized, therefore, the density of zirconia ceramic materials reaches its maximum around 3% (mole fraction).
3. What is high temperature ceramic powder coating?
The common types of high-temperature powder coatings mainly include the
1: Organic silicone coating: Using organic silicone resin as the base material, it has good high-temperature resistance, excellent weather resistance, and chemical properties. This type of coating also has corrosion resistance, insulation, and electromagnetic resistance.
2. High temperature polyester coating: Using polyester resin as the base material, it can maintain stability and durability in high temperature working condition. They also have good weather resistance, corrosion resistance, and chemical stability.
3. Thermoplastic powder coating: Using thermoplastic resin as the base material, it has good high-temperature resistance and flexibility, and can maintain good stability and durability in high-temperature environments. Thermoplastic powder coatings also have good weather resistance, corrosion resistance, and chemical stability.
4. Ceramic powder coating: mainly composed of ceramic particles, such as zirconium oxdie, alumina oxide, titanium oxide,silicon,chromium carbide,etc.
As a ysz powder chinese suppliers , we mainly supply plasma spray powder,that full name is 4mol yttria stabilized zirconia powder composed by 8% yttria stabilized zirconia powder. Well known for excellent flow, chemical homogeneity and structural integrity.It is best used for standard porosity (4 – 12 vol. %) TBC coatings.TBCs typically consist of a yttria stabilized zirconia (YSZ) ceramic coating layer that is applied over an oxidation-resistant metallic and non-metallic surface. The primary function of TBCs is to reduce the transfer of heat into the underlying base material, leading to improved mechanical properties and significantly extended component life. This technology has become instrumental in the pursuit of higher efficiency, reduced emissions, and enhanced engine performance of aerospace and industrial gas turbines.
Advanced TBCs find application on various critical components such as transition ducts, turbine combustion liners,Gas turbine, airfoils, heat shields, augmenters, nozzle guide vanes, and blades.etc.
4.China ceramic powder injection molding manufacturers
Zirconia ceramic material molding mainly includes three molding methods: injection molding, dry pressing molding, and isostatic pressing molding. As for which molding method to use, it mainly depends on the shape, quantity, and performance of the product. Different molding methods may also have slight differences in product performance.
4.1 Injection molding, refers to the molding method in which materials are plasticized in the heating cylinder of an injection machine, injected into the mold cavity of a closed mold by a screw, and cooled to form products. The principle of injection molding is to place the pellets in the material cylinder of the injection molding machine and heat them up, causing them to become viscous under shear force. Then, pressure is applied by a screw, allowing the melt to quickly enter and fill the mold cavity through the nozzle, and cool and solidify. The production process includes the following steps: mold closing → injection → cooling → mold opening → ejection of the product.
This molding process is mainly used for making small zirconia ceramic products and zirconium crown,etc.
4.2 Dry pressing molding,
Zirconia ceramic products for dry pressing forming is a forming method that uses pressure to press zirconia ceramic dry powder blanks into dense bodies in a model. Due to the advantages of zirconia ceramic dry pressing forming technology, zirconia ceramic dry pressing forming has been widely used in industrial ceramics and has achieved good results.
The use of dry pressing technology for zirconia ceramics has the following advantages:
1. The blank formed by dry pressing of zirconia ceramics has less moisture, higher pressure, and a denser body, which can obtain zirconia ceramic bodies with small shrinkage, accurate shape, and no need for vigorous drying.
2. The dry pressing process of zirconia ceramics is simple with a large production volume and few defects, making it easy to mechanize. Therefore, it is quite suitable for forming zirconia ceramic bodies with simple shapes and small and medium sizes.
3. The advantages of using dry pressing to form zirconia ceramics are accurate body size, simple operation, easy mechanization, low moisture and binder content in the dry pressed body, and small shrinkage during drying and firing.
4.3 Isostatic pressing molding ,abbreviated as CIP.
Zirconia ceramics have excellent properties such as high melting and boiling points, high hardness, insulation at room temperature, and conductivity at high temperatures. They are widely used in industrial production. So, what are the characteristics of isostatic pressing of zirconia ceramics products? Isostatic pressing molding is mainly used for zirconia ceramics with special shapes and large sizes. The blank body formed by isostatic pressing is uniformly and equally pressurized in all directions, and the pressure is high.
Therefore, the formed billet has high density, good uniformity, small shrinkage during firing, and is not easily deformed, cracked, or layered. This molding method can avoid delamination that is prone to occur during dry pressing, especially when making to mold thicker zirconia products.Therefore, this forming method is a commonly used method for producing big size and complicated shape zirconia ceramics products, but the blank body formed by isostatic pressing needs to be processed, which wastes some raw materials. At the same time, the processing of the blank body is relatively complicated, and the processing speed requirement is slow, resulting in low production efficiency.
Each molding process has its advantages and disadvantages.Choose each molding process based on the size and performance of zirconia ceramic products.
5. Zircon vs cubic zirconia
Zircon is also known as zircon stone.The chemical formula is ZrSiO4, and the phase is tetragonal crystal. It is belong to uniaxial crystal. Mohs hardness: 6-7.5, density:4.6-4.8.
Before the emergence of artificial cubic zirconia, zircon was the best substitute for diamonds. Zircon has strong birefringence, which means it has two refractive indices and a significant difference between them. As a result, a very special optical phenomenon has emerged. When observing polished zircon edge gemstones with a magnifying glass, a clear double shadow can be seen from the top surface and edge lines at the bottom. And diamonds, because they are “homogeneous bodies,” have no double shadow phenomenon.
Cubic Zirconia, abbreviated as CZ,the chemical formula is ZrO2.It is belong to isometric. Mohs hardness: 8.5, density:5.8.
Many jewelers refer to another type of artificially synthesized gemstone as “zircon”, which real name is cubic zirconia. Many jewelers, when they often refer to zircon, actually mean cubic zirconia, not natural zircon. The zircon series written is actually CZ in English. Zircon and cubic zirconia are two completely different things. Cubic zirconia was first developed by the Soviet people and is commonly known as the “Soviet artificial fake drill”. Also known as “cubic zirconia” or “Soviet diamond”, it is a type of zirconia crystal. Zirconia naturally exists mostly as monoclinic crystals, mainly in the form of mineral “clinopyroxene”. Zirconia, which exists as a cubic single crystal, is extremely rare in nature, but it is often synthesized artificially and widely used as a substitute for diamonds. The density of cubic zirconia is quite high, with a specific gravity of 5.6 to 6.0. Its hardness is 8.5, which is lower than diamond but already exceeds most natural gemstones. Its refractive index ranges from 2.15 to 2.18, and its surface has a diamond-like luster. The dispersion index ranges from 0.058 to 0.066, surpassing that of diamonds. Cubic zirconia has no cleavage and a conchoidal fracture, making it fragile. Under short wave ultraviolet light, it exhibits yellow and yellow green fluorescence, while under long wave ultraviolet light, the fluorescence is not significant.
Synthetic cubic zirconia is a type of artificial gemstone, not a natural gemstone, but a common substitute for diamonds. Therefore, zircon is usually referred to as it, so it must be clearly distinguished from the natural zircon.
6. Zirconium crowns
Zirconium crowns generally are produced by injection molding techniq.
In the form of white 3mol yttria stabilized zirconia powder,YSZ powder can be easily molded and pressed, resembling natural teeth. Therefore, it is used as an important component of dental bridges, veneers, and crowns. This material is also used for electrical devices and tableware. Dentists appreciate zirconia because it combines aesthetic appeal with the metal strength required for restoration. In addition, advances in technology and dental care tools have helped dentists fully utilize zirconia. The restoration made of this all ceramic material provides true teeth, such as texture, coloring, and translucency. The only drawback of this material is the lack of support for color customization.
Yttrium stabilized zirconia powder for making biological grade dentures has the characteristics of high fracture strength, high fracture toughness, and high transparency. It has a strong texture, high whitening ability, and can match the color of human teeth very well.
As ysz powder chinese suppliers in China, we can supply full particle size 3mol yttria stabilized zirconia powder for making zirconia dental application, including zirconia dental block, teeth bridge,and other biological products. With radioactive free and good biological compatibility, Kingda Ceramic 3mol ysz powder has flexible binder content or according to request of client, and suitable for various forming technologies,such as injection molding, dry press, CIP ,etc. The powder particles are evenly distributed, which can reduce the processing collapse caused by uneven density contribute to good connectivity of stacking pores, high affinity with coloring solution.
7. Zirconium vs zirconia
Zirconium is a chemical element with the symbol Zr and atomic number 40. It is a transition metal that is found in various minerals, primarily in the mineral zircon (ZrSiO₄).
Kingda Ceramic also supply ZrSiO₄ powder which is mainy used in ceramic glazes and pigments, mainly for whitening, hardening, and improving wear resistance. It can make the surface of ceramic products smooth, uniform in color, and enhance their mechanical strength.
Physical Properties of Zirconium:
Appearance: Zirconium is a lustrous, grey-white, strong metal that resembles titanium.
Density: It has a density of about 6.52 grams per cubic centimeter.
Melting Point: High melting point of 1855°C (3371°F).
Corrosion Resistance: Zirconium exhibits excellent resistance to corrosion, particularly in acidic environments.
Zirconium is typically produced by the reduction of zirconium dioxide (ZrO₂) with magnesium in a process known as the Kroll process.Zirconia, or zirconium dioxide (ZrO₂), is a crystalline oxide of zirconium. It is not a metal but a ceramic material.
Zirconia is the main oxide of zirconium, which is mostly in a white state, odorless, tasteless, and difficult to dissolve in water, hydrochloric acid, and dilute sulfuric acid. It usually contains a small amount of hafnium dioxide(HfO2),but its chemical properties are not very active. However, it has a high melting point, high resistance, high refractive index, and low thermal expansion coefficient, making it an important high-temperature resistant material, ceramic insulation material, and ceramic shading agent. It is also the main raw material for artificial diamond which is also called synthetic cubic zirconia.
Zirconia is commonly used in architectural ceramic glazes, with a typical dosage of 8% to 12%. And as the main raw material for “underglaze white”, zirconia is a good coloring aid for yellow green pigments. If you want to obtain good vanadium zirconium yellow pigments, you must choose pure zirconia. Zirconia without radiation is a completely different substance from natural zircon. Natural cubic zirconia is highly sought after in its natural state, so all cubic zirconia on the market is artificially synthesized. Synthetic cubic zirconia is inexpensive and has good optical properties, making it a cheap and beautiful alternative to diamonds.
Industrial Uses:
Zirconium: More focused on applications requiring metal properties.
Zirconia: Focused on applications leveraging its ceramic properties.
In summary, while zirconium is a metal known for its corrosion resistance and use in high-performance applications, zirconia is a ceramic known for its hardness and use in various industrial and dental applications.
8. How hot can powder coat withstand?
Powder coating is known for its durability and resistance to a variety of environmental factors, including heat. The heat resistance of powder-coated surfaces depends on the type of powder coating used. Here are the general temperature ranges for different types of powder coatings, such as Powder coating is known for its durability and resistance to a variety of environmental factors, including heat. The heat resistance of powder-coated surfaces depends on the type of powder coating used. Here are the general temperature ranges for different types of powder coatings, such as epoxy powder coatings,polyester powder coatings,silicone-based powder coatings,thermal barrier coating,etc.
Kingda Ceramic mainly supply thermal barrier coatings ,also refereed as TBCs which typically consist of a yttria stabilized zirconia (YSZ) ceramic coating layer . They are hollow spheres shape in the SEM .The main function of TBCs is to reduce the transfer of heat into the underlying base material,aim to improve mechanical properties and significantly extended component life.
Our this type of yttria stabilized zirconia powder for thermal protection, it can resistant temperature up to 900℃(1650℉).
Historically, thermal barrier coatings from have been plasma sprayed with the Oerlikon Metco 204 yttria stabilized zirconia (ZrO2 8Y2O3) family of powders for ceramic top coats , it can resistant about 1350℃(2460℉).
9. Nano yttria zirconia powder zro2&y2o3 suppliers
Zirconia can be divided into many types, such as yttrium stabilized, magnesium stabilized, cerium stabilized, etc., depending on the stabilizer used; According to different making powder processes, it can be divided into coprecipitation method, sol gel method, hydrothermal method, hydrolysis method, etc.
Kingda Ceramic just supply nano yttria stabilized zirconia (YSZ) powder which is a critical material in various high-performance applications, ranging from advanced ceramics materials,thermal barrier coating system, to cutting-edge medical devices. Kingda Ceramic suppliers of YSZ powder offer high-quality products that meet the stringent requirements of diverse industries.
Our ysz powder from 3mol to 8mol (different molar ratios), most powder belong to sphere shape,agglomerated & sintered.
Ceramic powders come in various types, each with specific properties tailored to different applications. Some common types include:
YSZ Powder: Known for its excellent mechanical properties and thermal stability.
Monoclinic Zirconia Powder: Used for applications requiring high strength and toughness.
Tosoh YSZ: A premium brand of YSZ powder known for its high quality and consistency.
As a technological breakthrough, YSZ powder surpasses the strength limitations of traditional fine ceramics. Because of the heat insulating properties and oxygen-ion conductivity, zirconia has potential for use in a wide variety of applications – everything from telecommunications to the new energy of the future and environmentally friendly products.
By understanding the properties and applications of these powders, manufacturers can optimize their processes and achieve superior results. Kingda Ceramic YSZ powder injection molded components and YTZ grinding media complete the product offering.
10. China zirconium silicate zrsio4 powder
The zirconium silicate,the main chemical formula ZrSiO4. It is an inorganic compound that is a silicate of zirconium and it exists in the form of zircon in nature. Zirconium silicate is usually colorless, but some impurities can cause it to color. It is difficult to dissolve in water, acid, alkali, or aqua regia. Its Mohs hardness is 7.5
zirconium silicate zrsio4 powder is made of high-purity zircon sand concentrates by process of ultra-fine crushing and grinding, iron removal, titanium processings surface modification, etc., and is a good-quality and cheap ceramic glaze emulsifiers, whitening agents, anti-seepage agents, and stabilizers.
The zirconium silicate has good chemical stability, is insusceptible to ceramics firing atmosphere. It can obviously improve the glaze-body bonding performance of ceramics and the hardness of ceramic glaze, and is widely used in the production of various building ceramics, sanitary ceramics,domestic ceramics, first-class ceramic art-ware,etc. Meanwhile, the zirconium silicate is further applied to color picture tubes in television industry,eniulsification glass in glass industry and production of enamel glaze materials. Zirconium silicate has also been further applied in the production of color picture tubes in the television industry, emulsion glass in the glass industry, and enamel glazes. Zirconium silicate has a high melting point of 2500 ℃ (4532℉), so it is widely used in refractory materials, zirconium ramming materials for glass kilns, castables, and spray coatings.
When high-performance zirconium silicate powder has the two conditions of whitening and stability, its performance in terms of zirconium silicate powder, particle morphology, particle size range, dispersion performance in the medium, and turbidity segregation after brick or glaze application is superior to conventional zirconium silicate.
The whitening effect of zirconium silicate is due to its formation of clinopyroxene after ceramic firing, which scatters incident light waves. This scattering is generally referred to as large particle scattering or Mie scattering. Based on theoretical calculations and actual powder production conditions, controlling the partilce size d50 value of high-performance zirconium silicate below 1.4um and d90 below 4.0um (measured by a Japanese laser particle analyzer) will result in the best opalescent whitening effect. Type A8L from Kingda Ceramic zirconium silicate powder can totally meet that requirements. In the whitening effect of zirconium silicate, a concentrated particle size range is important, and it is required to achieve a narrow distribution of particles as much as possible during the grinding process of zirconium silicate.